[ CPI Coalescers ]
The process principle
CPI (Corrugated Plate Interceptor) or TPI (Tilted Plate Interceptor) separators are predominantly used in separation of free oil from effluent water or suspended solids for oily water treatment in oily water systems in order to save space and improving efficiency compared to API separators.
The principle of difference in gravity between the phases (liquid – liquid or solid – liquid) is the basis of the separation of the two phases (Gravity Separation).
The effectiveness of this technique is affected by various factors such as difference in the density, viscosity, temperature, turbulence, and also the nature of impurity etc. and in some cases chemical coagulation and flocculation is needed to improve the separation.
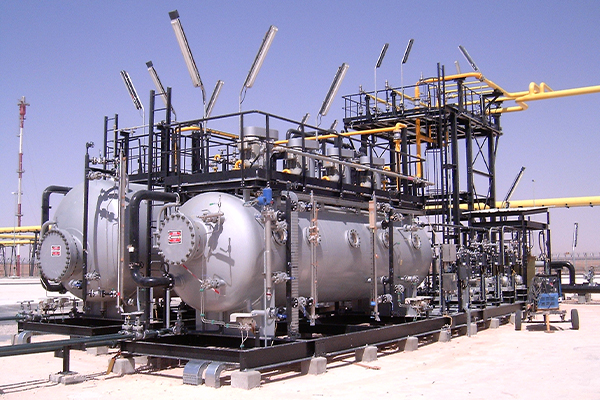
Unidro CPI equipment
Unidro provides engineered units, designed case by case to fit all process and project requirements.
When the stream to be treated is Produced Water, CPI has to be installed in closed drum, normally blanketed with fuel gas or nitrogen to prevent oxygen from air to dissolve into the water. The drum can be an atmospheric tank or, when the downstream system requires feed pressure, the unit shall be installed in pressure vessels.
Material selection for vessels and for corrugated plate packs is carefully evaluated for each case in order to prevent corrosion and guarantee equipment lifetime even in the severe conditions occurring when produced water is handled. PE, GRP, SS, special alloy steels are the available choices for the plate packs to meet each project requirements. Vessels may be lined or metal internal surface may be properly designed including corrosion allowance and/or sacrificial anodes.
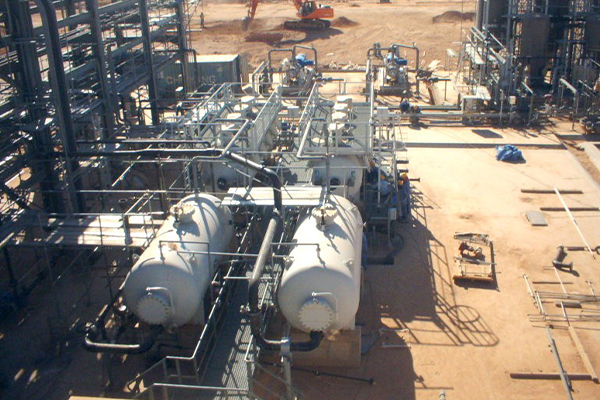